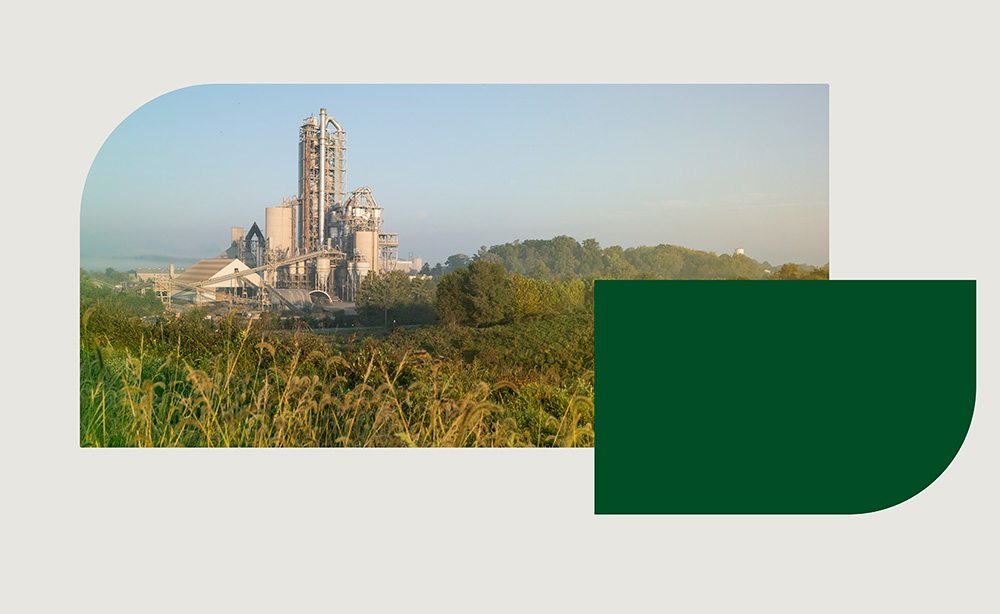
A building materials company for our future.
Heidelberg Materials North America
Lehigh Hanson is now Heidelberg Materials. In North America, Heidelberg Materials is a leading supplier of cement, aggregates, ready mixed concrete, and asphalt with more than 450 locations and approximately 9,000 employees.
Material To Build Our Future
We're dedicated to our goal to create sustainable value with industry-leading products and solutions to satisfy the construction needs of our customers around the world. See how we are Building a Better Future for our people, our customers, our communities and our shareholders.
Sustainability
Heidelberg Materials is committed to leading the development of sustainable solutions for built environments.
Digital
With advances in customer technology, Heidelberg Materials is driving efficiency and innovation in construction.
Products
Whatever building material you’re looking for, Heidelberg Materials is your trusted North American supplier.