Slag Cement
Slag cement, made from steel-making byproducts, enhances the strength and durability of concrete while reducing waste, energy use, and greenhouse gas emissions.
Slag cement is used in concrete for virtually any construction application, either in conjunction with traditional portland cement or Portland limestone cement (PLC) as a separate component. Slag cement can also be a part of a blended cement, such as ASTM C595 type IS or IT. In most use cases, slag cement replaces part of the portland cement in concrete mixes.
According to the Slag Cement Association, incorporating slag cement as a supplement in concrete offers higher strength, reduced permeability, and improved resistance to chemical attack. And as a recycled material, its production requires far less energy and natural resources than the conventional cement it partially replaces.
.jpg?sfvrsn=453e55fa_6)
Partner with an Award-Winning Slag Cement Producer
The Slag Cement Association annually awards projects that demonstrate slag cement's role in creating strong, long-lasting structures. As one of the top slag cement producers in the US, Heidelberg Materials is proud to be awarded for quality work that sets a precedent of excellence.
Race Street Bridge - Infrastructure Award
Whitman-Walker at St. Elizabeth's Max Robinson Center - Architectural Award
Heidelberg Materials is your trusted North American slag cement supplier. We also produce a range of other cement products and supplemental cementitious materials (SCM) like fly ash. The availability of products varies by region – use our Location Finder to find cement products and other building materials near you.
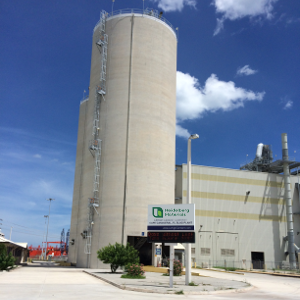
Recycling an Industrial Byproduct
Slag cement begins with the production of iron. The heart of the process is the blast furnace that refines iron ore into iron. The ingredients are heated to nearly 1500 degrees Centigrade to form two components: iron and molten slag.
The iron is used to produce steel, and the molten slag is converted to a cement-like material by quenching it with water. This rapid cooling creates glassy granules, which are then ground into the fine powder known as ground granulated blast-furnace slag (GGBFS) or slag cement.
Slag cement can account for 30% to 50% of the cement content in concrete mixtures. For applications such as mass concrete, deep foundations and in marine environments, that figure can rise to more than 70%. With cement replacement rates to these levels, slag cement is showing the most sustainable option for low carbon concretes.
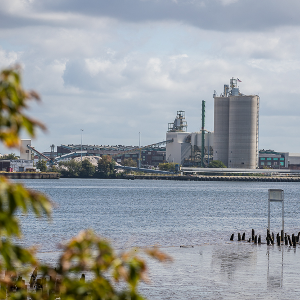
Environmental Benefits of Slag Cement
Slag cement is used in nearly all types of concrete construction: pavements; structures and foundations; mass concrete (i.e., dams and retaining walls); and prestressed, dry cast and precast concrete products such as pipes, pavers, and blocks. Today, slag cement is the best option for a concrete producer to use for the lowest possible low-carbon concrete mixtures.
Advocates point to several ways in which slag cement makes concrete better and more consistent:
• Easier to place and finish
• Higher strength
• Lower permeability
• Better resistance to corrosive chemicals
• Lighter color than conventional concrete (better architectural and decorative finishes)
Slag cement brings an impressive set of environmental benefits in line with the push for more sustainable construction.
First and foremost, it’s a recycled product – created from blast-furnace slag otherwise destined for disposal. The energy, emissions, and raw materials required to produce slag cement is a fraction of that needed for traditional portland cement.
Replacing a portion of portland cement with slag cement – typically from 30% to 50% – significantly lowers the environmental impact of concrete.
Another sustainability factor of slag cement is its nearly white color. Lighter-colored concrete has greater reflectance and visibility, which reduces the energy needed to light streets and parking lots at night.
Higher reflectance also mitigates the heat island effect, whereby highly developed urban areas tend to absorb heat and experience higher temperatures. Light-colored buildings and pavements reduce the energy needed for cooling and therefore lowers nearby ozone levels.
The Environmental Protection Agency recognizes the environmental benefits of using slag cement in concrete. It has classified slag cement as a “recovered" product under the Resource Conservation Recovery Act and has issued a procurement guideline requiring its specification on most federally-funded projects.
Our commitment to sustainability and low-carbon concrete motivates us to focus on growing the availability of GGBFS and other more sustainable cement products that comply with applicable CSA, ASTM, AASHTO or API Standards. Learn more about Heidelberg’s efforts toward a future built with more sustainable concrete.
Slag cement requires nearly 90% less energy to produce than portland cement. According to the Slag Cement Association, substituting 50% slag cement for portland cement reduces greenhouse gas emissions by more than 40% and lowers the embodied energy of concrete by more than 30%.
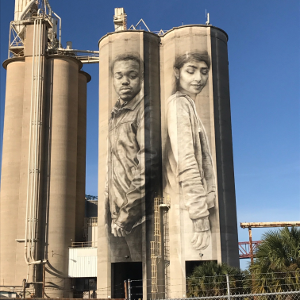
Resources and More Information About Slag Cement
Heidelberg Slag Cement Product Data
EPA Comprehensive Procurement Guidelines
Information on applications, uses, and benefits provided by the Slag Cement Association
Guidelines on the use of slag cement in pavement construction from the Federal Highway Administration