Combining portland cement with supplementary cementing materials (SCMs) produces blended cements. The materials are combined by grinding them together as part of the cement manufacturing process or by blending them together after grinding.
The supplements replace some of the portland cement with materials that are often recycled byproducts from other industries. Their environmental benefits are compelling: reduced waste, energy use and greenhouse gas emissions while conserving natural resources.
The most common supplements in blended cements are fly ash, slag cement and limestone.
Easily the most widely used supplementary material, fly ash is a byproduct of coal combustion in electric power plants. The fly ash is filtered out of exhaust gases as a fine powder.
Slag cement
is the byproduct of steel production. It is formed by the molten slag in blast furnaces used to process iron ore to make steel.
Finely ground limestone can replace 5% to 15% of portland cement. Portland-limestone cements require less energy to produce because the limestone is not pyroprocessed like the portland cement it replaces. Our Heidelberg Materials Company brand for this blended cement is EcoCem®.
Heidelberg Materials North America’s most popular blended cement is EcoCem PLC ™ in the US and EcoCem® PLC in Canada. At a couple strategic locations we are able to offer an EcoCem®PLUS, a blended slag cement (ASTM 595 Type IS) or a fly ash blended cement (Type IP) or a portland limestone fly ash blended cement (Type IT). In Canada, blended cements fall under CSA 3000 and the portland limestone fly ash blended cement is names a General Use Limestone Blended Cement (GULB).
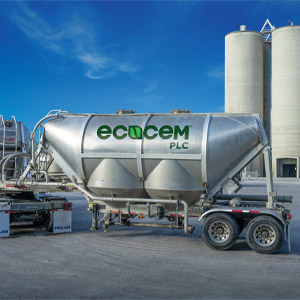
Raising the Bar for Cement and Concrete
The benefits of blended cements fall into two broad categories: environmental and performance-related. Using supplementary cementing materials can make concrete more durable, increase strength and influence other properties. They also contribute to sustainable construction by conserving natural resources and lowering energy consumption and emissions. The Global Warming Potential (GWP) to our blended cements are among the lowest in North America.
See Edmonton Plant EPD (EcoCemPLUS)
See Evansville Plant EPD (Type IS40)
See Delta and Mitchell Plants (EcoCemPLC)
Among key benefits:
Greater durability and long-term strength: Blended cements contribute to the long-term strength gain of concrete. Using SCMs in blended cement makes your concrete improve its resistance to chemical attacks. These supplementary materials contribute to a tighter concrete matrix reducing concrete permeability and shrinkage.
Lower heat of hydration and less risk of thermal cracking: If temperature differences between the concrete surface and its interior are high, cracking can occur. Blended cements reduce heat of hydration and thermal stresses.
Advances sustainable construction and lowers environmental impact: Recycling byproducts such as fly ash and slag reduces waste, conserves resources otherwise used to produce portland cement, saves energy and reduces emissions. These environmental benefits are transparent in our Environmental Product Declarations (EPDs).

Products and Standards
Blended cements conform to American Society for Testing and Materials (ASTM) C595, Specification for Blended Hydraulic Cements.
ASTM designates four types of blended cements:
Type IS (X), Portland-Slag Cement: Blends containing up to 70% slag cement are used for general construction.
Type IP (X), Portland-Pozzolan Cement: Used for general construction, this blend can contain up to 50% pozzolan. Fly ash is the most common pozzolan used in blended cement.
Type IL (X), Portland-Limestone Cement: Relatively new to the U.S. market, portland-limestone cement contains between 5% and 15% percent interground limestone.
Type IT, Ternary Blended Cement: Ternary cements are blends two complementary supplementary materials such as fly ash, slag cement or silica fume.
The highest amount of material in the blend determines its type. For example, if fly ash were the highest component, it would be considered Type IP.
The "(X)" in the designation refers to the percentage of the ingredient included in the blended cement. The remainder is portland cement. For example, Type IL (10), portland-limestone cement, contains 10% limestone and 90% portland cement.
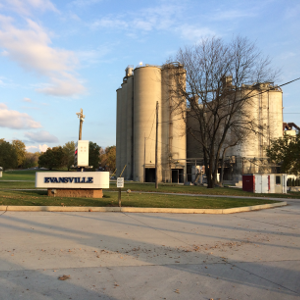
Resources and More Information
American Society for Testing and Materials (ASTM) C595, Specification for Blended Hydraulic Cements.
https://www.astm.org/Standards/C595.htm
Portland Cement Association publishes resources on blended cements and supplementary cementing materials
http://www.cement.org/cement-concrete-applications/concrete-materials/supplementary-cementing-materials