Why Concrete Pipe?
People prefer concrete pipe for its durability, its inherent strength, and for being risk-averse to proper placement. The life cycle cost of concrete pipe proves that it is cost-effective and should be demanded for the infrastructure of the future.
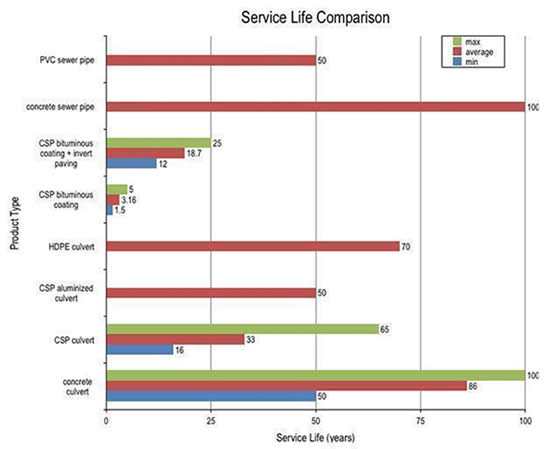
Durability
Concrete pipe has an extensive track record of performance. The first recorded concrete pipe sanitary sewer in North America was installed in 1842 in New York. But rigid pipes have been in service worldwide since 4000 BC.
Since 1842, concrete pipe has been a staple of North American construction. Because concrete pipe is such an established product, we can say with confidence that properly designed concrete sewers and culverts will perform for the design life of the project. On the other hand, competing products can only speculate what their longevity might be, due to their short service history.
When compared to other piping materials, concrete has superior impact and fire resistance. Concrete pipe is also not susceptible to long-term creep or UV degradation, problems characteristic of plastic pipes.
In addition to the superior physical properties of the material, concrete pipe is stiffer and has more inherent strength than flexible pipes such as PVC, HDPE and CSP.
Due to their reliance on the surrounding soil to carry the majority of the load, flexible pipes are more prone to stresses and failures, during and after installation, and can be adversely affected by excavations close by.
The graph to the right shows service lives, independently determined by the National Research Council of Canada, for many gravity pipe materials. Concrete pipe has the longest service life. In fact, the Cloaca Maxima (Ancient Rome’s famous sewer system), was created around 600 BC. Parts of this civil engineering wonder are still in use today, over 2600 years later. Not many products can claim to have such a proven track record of durability.
How Strong is Concrete Pipe?
Strength
Unlike other piping materials, concrete pipe has high inherent strength and actually gains strength over time. This is in stark contrast to flexible pipe materials such as PVC, HDPE, and corrugated steel, which have little inherent strength and rely instead on surrounding compacted soils. The video below shows just why concrete pipe is the preferred option when strength is a consideration, as is almost always the case in construction.
Risk Aversion
Concrete pipe derives most of its strength from the pipe material itself, not the surrounding soil. This means that the structural performance of the pipe is the concrete pipe supplier’s responsibility. Consequently, risk to the designer and installer
is minimized. Flexible pipe has little inherent structural strength. In fact, the majority of strength in flexible pipe is built on-site in the soil envelope. As incorrectly installed flexible pipe is prone to failure, the structural performance
of the installed flexible pipe (and the risk that goes with it) is taken on almost exclusively by the designer and installer.
The educational journal Structural Deformation Characteristics of Installed HDPE Circular Pipelines shows
how flexible pipe tends to fail at an alarming rate. In fact, the study shows that 63% of the 98 pipelines tested had deformation in excess of the specified limit. In addition ovality, crown flattening, buckling, and inverse curvature (snap through)
failures were observed. Specifying and installing concrete pipe is an excellent way to avoid unnecessary risk and dependence on the quality of installation.
Flotation of Concrete Pipe:
When water is displaced, an upward force - called buoyancy - is created. If the buoyancy force created by the displaced water is greater than the weight of the object displacing the water, flotation will occur. For all pipe, the buoyancy force depends on the weight of the pipe, the weight of the liquid load carried within the pipe, the weight of the backfill above, and the weight of the displaced water. Compared to other pipe materials, the significantly greater mass of concrete pipe is a benefit when installing pipe where flotation may be a problem. For more information, click here.
Sustainability
Concrete pipe has been determined to have the lowest global warming potential (GWP) when compared to commonly used pipe materials for water and wastewater pipelines.
“Life Cycle Analysis for Water and Wastewater Pipe Materials link to Life Cycle Analysis”,
a 2013 paper published by the American Society of Civil Engineers, reported on details of a Life Cycle Analysis of various pipe materials through four phases: pipe production, transport, installation, and use. The result: concrete pipe resulted in
the lowest GWP across the entire range of pipe sizes investigated.
The Life Cycle Cost of Concrete Pipe
Life cycle cost analysis (LCCA) is a tool used to compare the total costs of an asset or alternative throughout its life cycle. Costs in the analysis include initial capital costs (e.g. planning, design, construction etc.) and all future costs (e.g. inspection, maintenance, rehabilitation, replacement etc.). Costs are assigned to all future activities occurring in the analysis period, and these future expenditures are then converted into present day dollars.
Why Is It Important
LCCA brings all costs of each alternative to a common point in time to achieve a fair comparison. LCCA can readily identify the option with the lowest total cost based on present value of all initial and future costs. The most economical option in the long term is not always the option with the lowest capital or initial costs. When whole-life cost of an asset or alternative must be considered, an LCCA should be performed to determine the most economical route.
How Does LCCA Relate To Rigid VS. Flexible Products?
An LCCA can be performed to evaluate several competing products or replacement strategies. Often, it is efficient to choose, or award, one competing option over another based on lowest initial costs. But this may not be the most cost-effective decision.
An example of this is a new culvert installation or replacement. A flexible product, such as corrugated steel pipe (CSP), may appear to cost less to install than a rigid product such as precast concrete pipe (of course, this is not normally
the case where flexible pipe is installed in strict accordance with manufacturers’ recommendations). Initial material costs may also be less for the flexible product. However, an LCCA can illustrate how choosing the option with the lowest initial costs is not always the most economical option.
The total whole-life costs of the flexible product will almost always exceed the whole-life costs of the rigid product. The flexible product bears future costs of several rehabilitations and likely replacement, so it will outweigh the higher initial costs of the precast concrete pipe. Precast concrete pipe, unlike the CSP pipe, will have a longer service life (up to 100 years or more), resulting in less repairs and no replacements.
View A Life Cycle Analysis for Water & Wastewater Pipe Materials